The dental laboratory is the most important place in the dental clinic where dentures are made. But when a person goes to a dentist for a denture – crown, bridge, partial denture, etc., he or she hardly thinks about the nuances of making it. To get an idea of where and how dentures are made, we suggest getting acquainted with a modern dental laboratory – its structure and equipment, requirements for equipment and staff.
What Is a Dental Laboratory
Dental laboratory is a full dental department where dental prostheses of any complexity are made, and subsequently orthopedic constructions can be fixed both on natural teeth and implants, as well as on completely edentulous jaws. Why do you need a dental laboratory? Here it should be understood that prosthetics in modern conditions is a rather expensive process that requires qualified personnel (dental technicians), high-precision equipment, which also costs a lot of money. Therefore, the fabrication of dentures must take place in certain conditions, in compliance with all technological and hygienic requirements.
It is also worth mentioning that dental technicians (sometimes also called lab technicians, although we would rather call them jewelers!) are not only involved in the fabrication of dentures. Such an important field as orthodontics can’t do without these specialists, either. Orthodontic alignment and replacement plates, therapeutic, prophylactic and athletic mouth guards, and a number of other devices are also made by dental technicians.
How dental laboratories are organized, who works there, what equipment they have and what they make – this is our article.
What Are Modern Dental Labs Like?
Here we distinguish between 2 main types, which can be either independent or located directly in the clinic:
- Independent laboratories: these organizations are independent of any clinic and cooperate with orthopedists, orthodontists and implantologists of different dental medical centers, or doctors working individually in small offices. Self-employed organizations are quite large, with a large staff that produces all kinds of dental restorations for thousands of patients a year. The largest organizations take orders not only from their city, but also from the region, from other cities in the country – depending on the fame of the company, equipment and the number of orders,
- Dental laboratory at a large private dentistry or public clinic: In this case, dental technicians focus mainly on customized work for the patients of a clinic or dental network. Naturally, if the division is not fully loaded with “in-house” orders, technicians may take on outside work (from other medical centers) to increase their salaries and the company’s overall profits.
In any case, all preparatory work, such as turning, taking impressions and sending them for the production of a dental design of the selected type is performed exclusively by the attending physician (orthopedist, orthodontist).
Requirements for Such Laboratories and Dental Technicians
- license: when working with jewelry and medical centers,
- sterility, ventilation and good lighting of offices and work areas,
- availability of all necessary equipment: it must have manufacturer’s certificates of conformity and be serviced regularly,
- provision of staff: according to the standards, 1 senior specialist is assigned to 10 ordinary specialists in a dental laboratory,
- Diplomas and certificates for specialists, which confirm their training and advanced training,
- cooperation with licensed clinics of the city and other cities.
What Does a Dental Laboratory Do?
Modern dental facilities must be equipped with all the necessary equipment and tools to create orthopedic and orthodontic products of any known kind:
- Classic metal crowns and bridges: in spite of their low aesthetics, these prostheses are still used due to their low cost,
- Metal-ceramic, metal-free and ceramic crowns, and bridges: porcelain (as spraying), lithium disilicate, aluminum dioxide or zirconium. This is one of the most popular areas – quality and aesthetic,
- Ceramic inlays: a kind of “hybrid” of a filling and a partial crown,
- Removable orthopedic appliances: bow-tie, plate, Acry-free, Quattro Ti, partial dentures of any type (on hooks, clasps and telescopic crowns),
- Orthodontic plates,
- Veneers and ultra-crowns: these are designed for making a “Hollywood” smile (lumineers are not made in the laboratory – they are designed by Cerinate, and are sent to the clinic after being made individually for the patient),
- Prostheses and individual abutments for fixation on implants,
- Temporary crowns, bridges and complete orthopedic constructions,
- metal bars for implant fixation and metal-free frameworks.
How Is a Dental Laboratory Arranged?
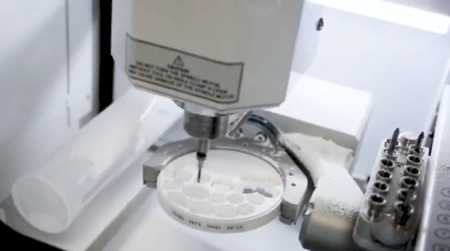
According to the requirements, the arrangement of each dental laboratory must include several rooms (rooms, offices). Some of them to save space or in the absence of conditions can be combined with each other. But there are also rooms that in any case should be isolated from the other rooms. Consider further the organization of the dental laboratory in detail.
Set of necessary equipment
Each room is equipped in accordance with the profile requirements. If we consider the arrangement as a whole, each organization must have the following standard equipment:
- ventilation system and fume hoods: for working with chemical or dusty substances,
- sets of tools for modeling for each technician,
- shake tables and plastering tables,
- vacuum mixer for mixing materials,
- plaster storage bins, water and plaster dispensers,
- articulator and occluder: the first device reproduces the movements of the lower jaw in different directions and the second fixes the prosthetic model in the position of central occlusion, simulates opening/closing of the mouth, facilitates placement of artificial crowns,
- Brass cuvettes and presses for cuvette compression and plaster pressing,
- Muffle furnace: melts the wax out of the metal frames (opacities) in which the components of the future denture are placed,
- drilling machines: for mechanical drilling (drills) or laser drilling,
- trimmer to trim the base of the plaster model of the jaw,
- curing machines: machines for heat treatment of plastics,
- soldering units or laser welders for metal components,
- machines for melting and casting metal,
- machine for grinding and polishing prosthetics: with a mechanical or electromechanical principle of operation,
- sandblaster and steamblaster: for treating and cleaning products
- thermoforming machine: for manufacturing of mouth guards, temporary crowns, guiding templates.
Private laboratories – independent or located in clinics, should also have a dental furnace for firing and pressing of ceramics, robotic CAD / CAM machines, 3D-printers, computers with special programs, analyzers HIP-plane. Because without this equipment it is impossible to create modern aesthetic solutions from different types of ceramics and zirconia or aluminum dioxides.
Basic or blanks room
This is where the main work is done – the most popular prostheses and orthodontic appliances are created, it also houses the workplaces of dental technicians. In large organizations, there may be several main rooms – they are subdivided according to the nature of the work performed, each such room is designed for no more than 15 employees. If we consider the gradation by type of the most common technological processes, we can distinguish the following main production areas (given below), which can be both located in separate areas of one room, and in specially designated rooms.
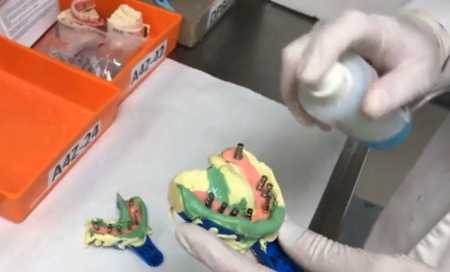
- For working with metals and precious metals
The main room has an apparatus on which metal blanks for crowns are produced and then they are coated with precious metal plating or veneered with ceramics. Precious metal crowns can also be made in the main room, but this material is dispensed in a special room with an alarm system (where the relevant rules for storage and dispensing of silver, gold, palladium and platinum are ensured). And the main office should have fireproof metal safes for storing blanks and finished products.
- To work with ceramics
The manipulation of ceramics requires the appropriate apparatuses. For example, a program-controlled electric furnace for firing and glazing ceramics has a display to control the temperature during the various production steps. In the electric furnace, ceramics processing stages such as drying, firing, ageing, and cooling take place.
In general, the work with ceramics (modeling, application of facing or pressing, etc.) requires maintaining certain conditions in the room – temperature, cleanliness, humidity, lack of drafts and surges in the power supply, cleanliness of working surfaces. Therefore, it is recommended that such work in a separate room. And if ceramics is processed by CAD/CAM-technologies, robotic milling machines must be located in a specially designated room (about this we will tell a little bit below).
- For mixing the molding mass
Here a vacuum mixer is used – a special unit with a bowl, where there is a mixing of the components for the molding mass, which then covered the wax blank of the future orthopedic product. If air bubbles remain in the mass, it will reduce the quality and durability of the future product, so before mixing air is pumped out of the bowl. It also helps to obtain a homogeneous mass without lumps, which can appear as lumps or growths on the orthopedic structure.
Standard vacuum mixer equipped with an electromechanical drive has 2 bowls (or containers) of different volumes and 2 operating modes (simultaneous vacuum + kneading, sequential vacuum pumping and kneading), an adjustable timer, digital diagnostics and indication, sound sensor.
- For sandblasting cast frameworks
Cast frameworks (fixed crowns, bridges or partial dentures) should be grit blasted to remove molding residue and scale to prepare the structure for the final manufacturing step. Powdered aluminum dioxide (and in the premium version, titanium dioxide) is used as the blasting material.
Inside the sandblaster housing there is a chamber (sealed) with a compartment for collecting aluminum dioxide and a nozzle device into which compressed air is supplied by a foot drive and sand is drawn in – and then the cast cage is blown. There are 2 openings on the body to which the lab technician’s hand gloves are attached, and there is a sight glass at the top to control the treatment. After processing, sand and dust are forcibly sucked out of the chamber, the product is extracted and sent to the next stage.
Specialist Workplaces
The dental technician’s workplace in the main rooms includes a table with various equipment and drawers, sliding and hinged shelves (a cabinet can replace them), where tools and parts of the fabricated items are kept. In general, the equipment of the dental technician’s workplace depends on the nature of the frequently performed work, labor safety requirements and ergonomics. If we consider a standard workplace, it includes the following items:
- A sturdy and stable table: made of wood or other material. The tabletop may be partially covered with a sheet of stainless steel or brass,
- a fluorescent lamp on the table to the left that provides a powerful, even light and does not distort the colors of the materials,
- electric spatula for waxing,
- dust collector: equipped with power regulator, dust collector and filtering system,
- Bunsen burner: for material heating on open fire – works on gas (from a bottle or from city networks),
- portable drill,
- sight glass with a magnifying glass: in addition to magnifying small parts, the glass protects the technician’s eyes from solid particles and dust (generated during machining),
- air nozzle: manual device for blowing the surface of the workpiece with a controlled jet of air,
- workbench with a tray where plaster waste, plastic and metal scraps are stored
- tool boxes: spatulas, pliers and tweezers of various sizes, a knife for working with plaster, scissors for metal cutting, anvil, hammers, jigsaw, files, sandpaper and tools for grinding/polishing, etc.
Special or auxiliary rooms
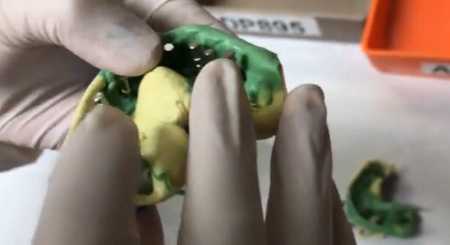
Special rooms are needed for work that emits hazardous substances, dust, toxic gases and fumes, soot or smoke. Or the nature of work with materials implies special care for these substances.
- Plastering room.
This is where the galvanized tables are located, on which plaster is mixed and modeled into jaw prototypes – for temporary and permanent orthopedic product models. The tables have holes where the plaster waste is removed (it goes into special containers). Sinks with cold and hot water are also connected to the tables, and the drains are equipped with special filters, which retain the smallest particles of material, so that the plaster does not clog the sewage system.
The plaster room also contains:
- sealed containers for storing different types of gypsum,
- Dispensers for water and plaster mix: wall and table-top,
- shakers, brass cuvettes and presses for them,
- gypsum sawing machine,
- apparatus for drilling and grinding of gypsum,
- device for trimming the plaster base: forming the contour of the plaster model.
The plaster room should have tool kits, articulators and occluders for each worker. Models of future orthopedic products are plastered in cuvettes, occluder or articulator (devices that allow you to create prosthetics in accordance with the correct clamping and movement of the jaws). Metal components are plastered before soldering.
- Molding and polymerization room
Various plastics (acrylic, monomer-free) and nylon work in this room. The plastic raw material or “dough” is kneaded on special smooth tables, shaped or packed into cuvettes using presses and polymerized – i.e. hardened under certain conditions. For example, polymerization under pressure in automated units or boiling in boiling water for 10-30 minutes. The latter method leads to the creation of high humidity in the room, so the walls and floor around the unit are covered with tile, and an exhaust system is installed over the container.
Also in the polymerization room are melting devices with wax catchers (for melting wax from the cuvette). And the remnants of soft plastic left over after molding are placed in an airtight bunker – to reduce air pollution by toxic fumes from methyl methacrylate.
- Foundry room
The casting room is designed for casting metal parts for orthopedic and orthodontic constructions. Casting is recommended in a fume cupboard by means of high-frequency induction heating units, which can melt any metal alloy or metal (even the most refractory). Melting machines are also equipped with a centrifugal casting function and special casting mold technology – during the casting process, the mold with metal rotates in different planes (vertical, horizontal, inclined) or along a complex trajectory.
The fume cupboard should contain the muffle furnaces required for drying and heating the molds, as well as for removing wax. Also here are installed apparatuses for sandblasting, grinders, boxes with metals for obtaining alloys, caster’s table, ceramic refractories (crucibles), components for mixing molding and facing masses.
- Soldering room
The soldering room must be equipped with powerful ventilation, designed to remove the smoke and combustion products produced during soldering. Ventilation is suitable for laboratory fume hoods – in their working area are installed muffle furnaces and soldering units, and directly in the upper zone is an “umbrella hood”.
Soldering unit is designed for soldering of metal elements of orthopedic and orthodontic devices, this device has a compressor for gasoline supply. Tanks of gasoline are stored away from heat sources. A muffle furnace is needed for burning wax, drying and firing the opoka (casting mold-billet). Also gilding, electrochemical polishing and bleaching of prosthetic constructions takes place in the brazing room.
- Polishing room
The polishing room is used for polishing and finishing of the finished workpieces before final placement in the patient’s mouth. If the dental unit works with precious metals, you need to have at least 2 polishing machines – for normal dentures and for those with gold, etc. The polishing mechanical units are equipped with dust collectors with an extraction system – so that the dust does not harm the lab technician and does not contaminate the product, but is immediately removed. After processing precious metals, polishing tools, metal chips and dust should be sent to the factory for recycling.
- Division with CAD/CAM systems
The production of dental crowns, inlays or veneers made of modern materials (zirconium dioxide or aluminum, lithium disilicate) requires specialized equipment. Here, CAD/CAM technology is widespread, making minimum use of human labor and maximum use of digital and robotic technology. The CAD/CAM department consists of 2 rooms:
Modeling room: digitized impressions of the jaw (obtained after scanning with a 3D scanner) are processed using computer programs, a virtual three-dimensional model of the prosthetic structure or a template is created,
Fabrication room: this is where the robotic machines are housed, the ceramics and zirconium dioxide are milled, and the metal beams for the implants are created. Also in this room are 3D printers for printing jaw models and surgical templates (on which implants are placed).
Auxiliary rooms include bathrooms, shower rooms, storage rooms, a staff lounge, and a storage room for items and supplies for cleaning the lab. Large organizations may also have classrooms for students and technicians undergoing advanced training.
What Manufacturing Methods Are Popular Today
In recent decades, scientific and technological advances have led to the automation and computerization of many areas of life, and industry. In the past, dental technicians made things by hand based on plaster casts – a long, multi-step process (and finished products often have errors) – but now CAD/CAM systems are gradually taking over. Yes, the equipment is expensive, but it is worth it for the precision and speed of fabrication of orthopedic structures, and modern materials for artificial teeth last 3-5 times longer. However, the vast majority of dental organizations in our country still work “the old way” – with plaster models, because they cannot afford to pay for the latest equipment and retraining of specialists.
How Prosthetic Constructions Are Made in the Dental Laboratory
The fabrication of a prosthetic restoration begins after the dental technician receives an impression of the patient’s jaw and the data on the assessment of central occlusion (a facial arch is used for this purpose) or the results of a digital scan. In the second case, the process of modeling and fabrication is done with the help of high-precision programs and machines, and here the specialist is more of an observer than a doer (because almost all the work is done by the machines, and a man only coordinates their actions). Therefore, we will consider the “manual” or classic method of fabrication of full dentures, which is carried out in several stages:
- A working model is created: a plastic impression-template (or matrix) is covered with wax and acrylic, a plastic bite roll and artificial teeth are placed on this matrix,
- Try-in the temporary model on the patient and check the occlusion data: this takes place in the orthopedist’s office. If there is any discomfort, the doctor can remove the excess plastic from the temporary model or send it to the technician for revision. If the model fits all the parameters after the first fitting, it is sent to the next stage of fabrication,
- fabrication of the permanent structure: the temporary model is placed in a mold, poured in plaster or plastic (to create a permanent base or gum analog), hardened and boiled in boiling water. After that, the wax is removed and the artificial teeth remain in their places in the model (as they will be in the finished prosthetic structure). The model is filled with pink-painted acrylic “dough,” pressed, and then beaten – so that the blank can be removed from the plaster,
- Finishing: The sharp edges of the artificial gums are grinded with a special wheel, and then the entire structure is treated with sand and wet pumice, and then polished until it has a natural luster. The prosthesis is then disinfected and sent to the orthopedist for delivery to the patient.
How Long Does It Take to Fabricate in-house or in a Third-party Lab
Production always depends on the workload of the dental office. Patients at clinics with a dental technology department have an advantage here, too, as they are considered to be “first come, first served”, i.e. they can wait a maximum of 3 to 4 days for the production of a new or an old prosthesis, and in some cases they can even make a temporary prosthetic restoration in just a few hours.
Patients who are treated at another clinic (without a dental department) wait at least 2 weeks for “new teeth” to be made or repaired. And the lion’s share of the time here is not the fabrication itself, but the transportation to and from the fitting. If several corrections to the temporary model are required, it can take up to a month or more.
Is the Orthopedic Shop Really That Necessary?
Why is it so important to have orthotics fabricated according to all requirements? Let’s look at an example – a patient goes to a small private dental office where the orthopedic surgeon makes the prosthetics himself (crowns, bridges, “butterflies,” etc.). In the best case scenario, the orthopedist will have only one room at his disposal, where all the stages of production take place – and some of the work will be done with a drill in the room where patients are treated.
Yes, such a product would be sold without a markup (as if it were made in a laboratory), but its quality would not be very high, because the main production steps are inaccurate, there is a risk of allergies or irritation – if dust from sanding or bacteria from tools, from the air remains on the product. Therefore, truly high-quality and safe orthopedic and orthodontic constructions can only be made in a specialized place, namely a dental laboratory.